Case study
Generative design of turbomachinery blades using autoencoders
High-resolution Computational Fluid Dynamic (CFD) simulations generate a huge amount of data, especially when considering the high-fidelity simulations often required in fields such as turbomachinery. These profoundly accurate flow field predictions are ultimately used to calculate performance metrics such as design efficiency. The Monolith AI platform can be used to create models which can be trained to predict these scalars from existing simulation results. The platform makes advanced machine learning techniques user-friendly, allowing engineers to get the most out of the data they have available.
In this case study, we will investigate how to use variational autoencoders as a generative design algorithm to first automatically parametrise existing blade designs as well as create new designs for given performance targets. So far, autoencoders have been mainly used in image processing for this purpose and their generative capabilities are regularly seen in the news as they can generate complex information such as realistically looking human faces (deep fakes).
The automatically found parameters (hyperparameters) of the blades can be used to increase the accuracy of machine learning models that are used to predict blade performance. The focus of this case study will be the optimisation of highly loaded transonic compressor blades (Rotor37) performed together with Rolls Royce and the University of Cambridge.
Autoencoders
Variational autoencoders are a specific type of Neural Network, designed to extract a (user-specified) number of latent parameters describing a given 3D geometry – in this case, transonic compressor blades. They were developed for image processing, and are newly applied to 3D design here. To learn more, check out this past post on The AI revolution: from image recognition to engineering.
A significant advantage of autoencoders is that they offer the possibility of visualising decoded geometries in real-time within the Monolith platform.
Autoencoder: the blade geometry is condensed in a set of latent parameters (encoder), the latent parameters are used to generate a new geometry (decoder).

Once trained, the latent parameters of the autoencoder (sometimes referred to as DNA of a geometry) can be used as an alternative parametrisation of the surface mesh. For a trained autoencoder, it is possible to investigate what each latent parameter represents by observing how varying the value of the specific entry changes the shape of the blade.
In general, autoencoders can be a powerful tool because the parametrisation found by the machine learning model offers a more accurate and efficient representation of the geometry than if it is done manually. For example, an advanced turbomachinery blade normally requires up to 100 parameters to describe its shape whereas the autoencoder here only needs 15. Using them to reduce the dimensionality of an optimisation problem is one of their main benefits.
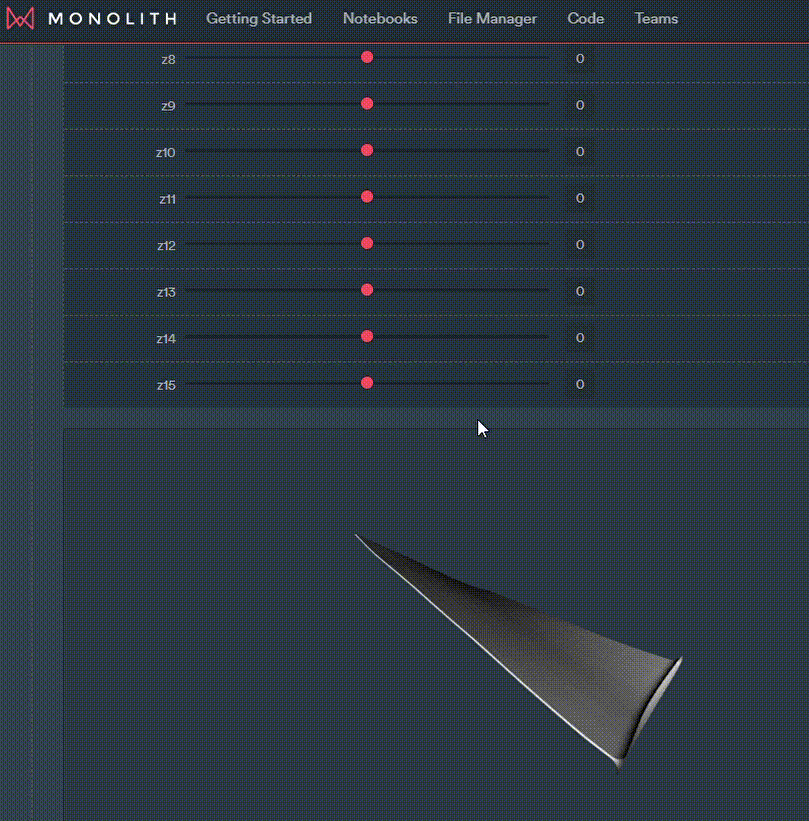
In a research paper written with Rolls Royce and the University of Cambridge, the autoencoder was first trained on a set of surface meshes of Rotor37 blades to find a parametric description for the compressor blades. The parametric description was then used, along with existing CFD simulation results, to train the models on blade geometries spanning the design space.
The autoencoder produced a parametric description that accurately captured the shape of the blades, and the use of output consolidation improved the accuracy of the efficiency predictions. For high-efficiency values, the Mean Squared Error (MSE) was reduced by over 50% compared to a Gaussian Process Regression predicting the efficiency directly from the parametric description of the blade.
The results of this ASME article indicated that autoencoders can be used to perform design optimisation with higher accuracy as well as reduce the dimensionality and therefore computational complexity of the optimisation problem.
Below: The original (blue) and decoded (red) geometries from the used test set.
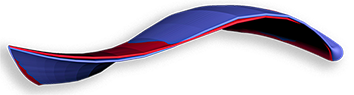