Case Study
Improve Surrogate Model Accuracy With Rolls Royce
A computational fluid dynamic (CFD) simulation can contain millions of data points, yet for some reason, almost all surrogate modelling algorithms currently used, such as radial basis functions, polynomial regression or Gaussian processes, only extract a few data points in post-processing and throw away gigabytes of flow field data.
In this article - written together with Rolls Royce and the University of Cambridge - we investigated if neural networks trained on the entire fields of CFD simulations and not just a few selected data points can increase the accuracy of a surrogate model for the same number of simulation runs. We call this process output consolidation, a method which allows to incorporate multiple relevant data sets into a single specific prediction. Initial results are promising: around 30% lower mean square error as the full flow field provides better information into outliers that the simplified metrics exclude.
The focus of this publication centres around the optimisation of highly loaded transonic compressor blades (Rotor37) and finds that the accuracy of the predicted Quantities of Interest (QoI) can be increased by using output consolidation. By employing Monolith AI, users can go beyond predicting simple scalar outputs, and instead make the most of the entirety of their resulting CFD data. Using a special Neural Networks architecture to predict some relevant field quantities, engineers can then use the field predictions to predict the performance metrics that they are ultimately the most interested in.
What is the idea behind output consolidation?
QoI's such as the pressure field, velocity profile or even integral values like the mass-averaged total pressure, total temperature, and swirl at inlet and exit of a turbomachine, are usually calculated from relevant outputs of a CFD simulation.
The method allows for the incorporation of multiple relevant data sets into a single specific prediction for a QoI. It uses two models in succession, in a way such that:
- The primary model predicts an intermediate quantity (related to the QoI) from the given scalar or geometry data, for example, the entire blade surface pressure field.
- The secondary model predicts the QoI by taking as inputs both the given data and the primary model predictions.
Modelling the intermediate quantities, which are used to calculate the QoI, is a way of incorporating more knowledge in the final machine learning model, that then becomes informed about the flow. In this study, the QoI was the adiabatic efficiency of the compressor blade, and output consolidation was carried out using the blade surface pressure.
Below: Figure 1: Connection between models in the output consolidation.
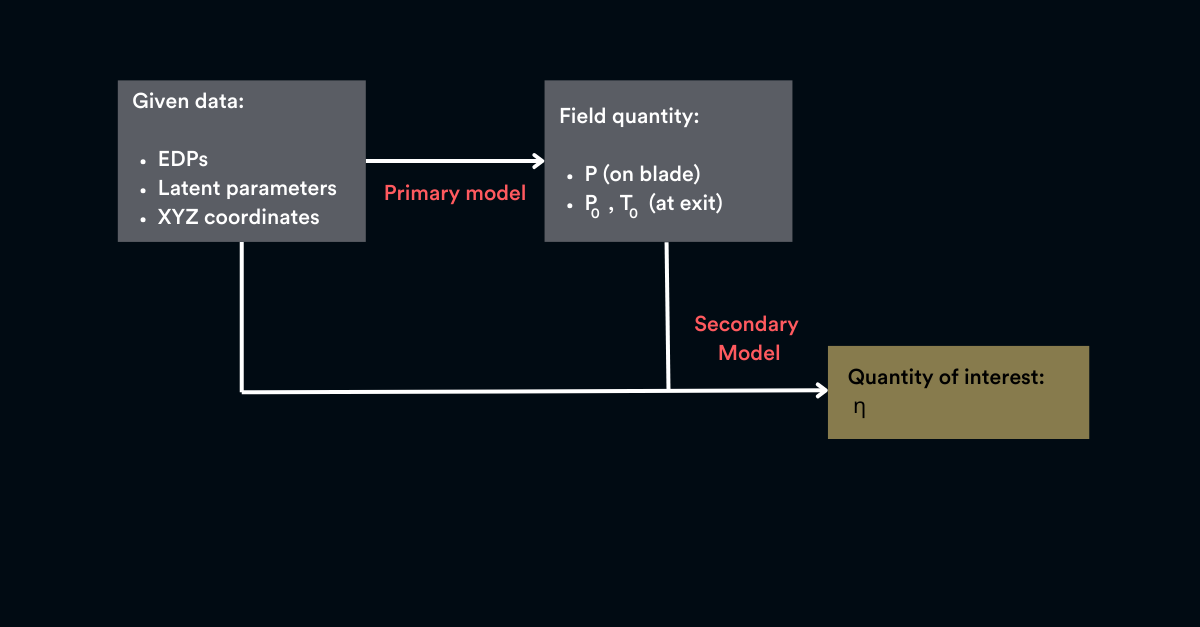
The consolidated model was then finally used to optimise the blade for maximum efficiency, by running a targeted optimisation (based on differential evolution) without any geometry constraints on the two tertiary models to maximise the QoI. Given a number of candidates in the design space, the evolutionary algorithm finds the optimal solution by iteratively combining attributes of the best candidates found in the previous step. The model identified a blade geometry that achieved, in a confirmatory CFD run, a 2.84% increase in efficiency compared to the datum blade.
Below: The values of the QoI as predicted by baseline and final models.
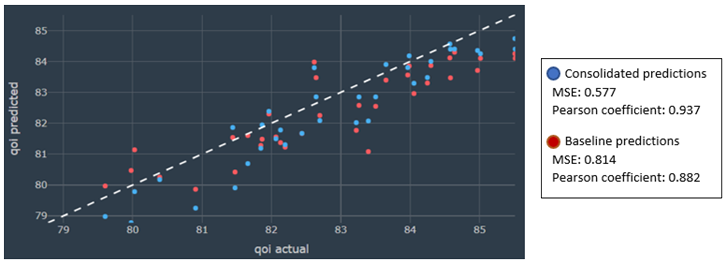
Results Using Monolith
The results of the Rotor37 case study indicate that the accuracy of the predicted QoI can indeed be increased using output consolidation. The prediction accuracy was increased within the range of QoI values that are important for the optimisation problem. In conclusion, utilising neural networks trained on flow field data seems to be a promising new technique to perform optimisation with a limited number of CFD simulations available.
While the results are promising, we need to further investigate the general applicability of this new approach needs to be conducted. For highly turbulent flow fields or extremely non-linear mechanical fracture problems, it is possible that learning the flow field will create non-physical local phenomena that could add unexpected non-physical behaviour into the solution space and increase the error. Approximating entire flow fields using physis-informed neural networks is still a very much open area of research.
One additional benefit of output consolidation is that it also opens new doors to reuse existing simulation data and extract from it information that is normally lost through direct optimisation of scalars. Imagine being able to keep data from expensive LES simulations by storing the field information in a neural network for future use.